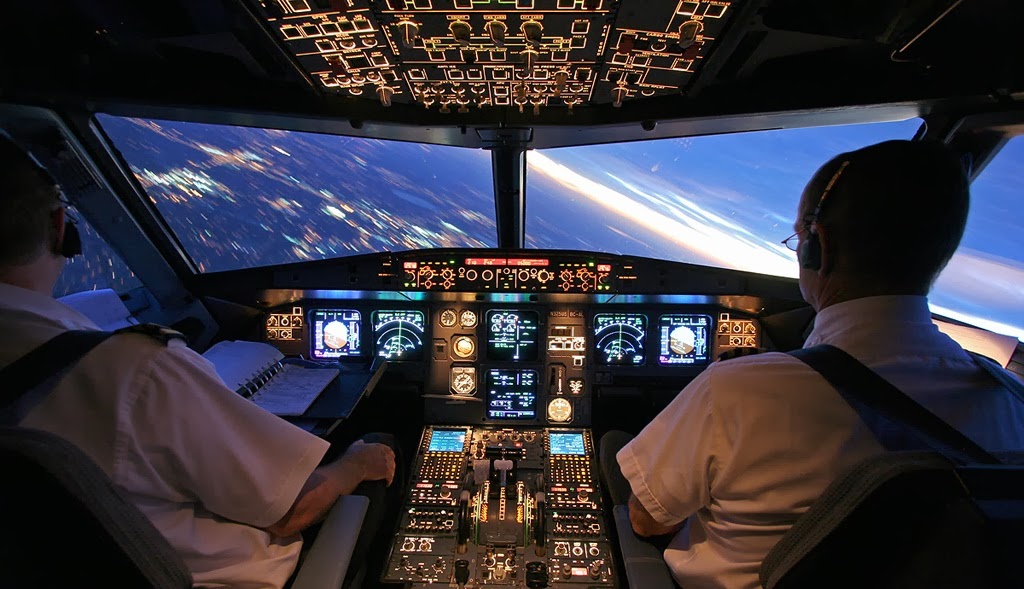
Airline LOSA
A Line Operations Safety Audit (LOSA) is a proactive, formal process that requires expert and highly trained observers to observe operations in real-time and to collect safety-related data on environmental conditions, operational complexity, and human performance on the flightdeck. Numerous airline and environmental threats exist in the operating environment. These threats can be due to weather, delays, maintenance, procedures, and more. LOSA is an ideal way to identify these threats and understand flightcrew responses. LOSA also reveals how errors and undesired aircraft states are managed by flightcrews.
LOSA is complementary to your Flight Data Monitoring (FDM) program. FDM provides excellent data, but the data are limited to the “what” as opposed to the “why” an event happened. LOSA is a great tool to complement your FDM data because LOSAs, which are conducted in real-time using trained observers, allow you to understand the “whys.” LOSA observers see firsthand what’s happening. For example, are unstablized approaches due to ATC issues? A Procedural problem? Checklist flow? These are things that FDM by itself cannot capture. But, by combining FDM with LOSA, you will have a much more robust picture, and thus can take a more pragmatic approach to corrective/preventive actions.
LOSA is not a checkride or a line check. LOSA is confidential and nonpunitive. LOSA is conducted by a non-threatening company employee (typically another pilot) who rides in the jumpseat taking notes on what is happening during the course of a normal flight. Once all the data are collected, then a report is written and recommendations are made to management to both reinforce the positives and improve the negatives. LOSA enables organizations to manage threats and errors so that those threats and errors do not turn into accidents and incidents in the future. With LOSA, you are being predictive—which is the ultimate form of proactive safety!
LOSA is highly recommended by IATA for airlines that intend to be listed in the IOSA Registry. The IATA Operational Safety Audit (IOSA) is the benchmark for global safety management in airlines!